pvd coating vs anodizing - anodized aluminum vs powder coating : 2024-11-02 pvd coating vs anodizing When it comes to choosing the right finish for your project, anodizing and powder coating are two of the most popular options. Anodizing provides a harder, richer-looking surface that is resistant to . pvd coating vs anodizingItem# 123000. 17 reviews | Add Review. Free Shipping (Orders Over $59) Allure women. Eau De Parfum Spray 1.2 oz. by Chanel (View All) Select Size. OZ to ML converter. eau .
$15.99
pvd coating vs anodizing
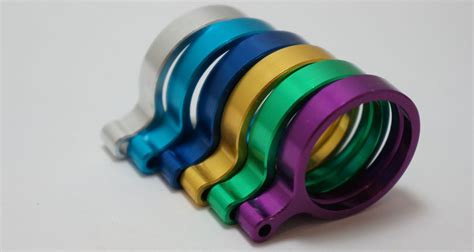
The primary difference between anodizing and powder coating lies in the coatings formed. Powder coating is an organic coating, or a coating containing carbon, while anodizing forms a metal oxide coating.This comprehensive guide dives into the nuanced differences between powder coating vs. anodizing, shedding light on their respective processes, visual appearances, durability, and environmental impacts. Powder coating and anodizing both produce durable, corrosion-resistant protective layers that make your product look great. Powder coating often offers a wider variety of color options. It hides . Short Summary. Comparing Anodized vs Powder Coat requires understanding the key differences in terms of durability, appearance and environmental impact. Anodizing provides greater .Table of contents Hide. 1 What is PVD coating? The Basic Principles. 2 The Science Behind PVD Coating. 3 PVD Coating methods used in industrial applications. 4 A step-by-step guide to PVD Coating. 5 .The entire PVD coating process is completed in the United States. Traditional chrome plating will almost always start to pit & peel within 12-24 months. Traditional chrome plating adds an average of 2 to 3 pounds per wheel. PVD Coating Vs. Other Coating Methods. Here’s a quick comparison of the PVD coating process and other similar techniques. PVD VS CVD Coating. . subject the substrate to pretreatment, like . Physical vapor deposition (PVD) coatings offer many of the same benefits and, in some ways, are superior to hard chrome. Physical vapor deposition (PVD) describes a variety of vacuum deposition methods that can be used to produce thin coatings. PVD is typically used to coat components at relatively low coating temperatures of 160-500°C. Additionally, electroplated coatings may contain impurities from the plating bath, while PVD coatings are pure since they are evaporated from a solid source material. 4. Cost and Efficiency. Cost and efficiency are also significant differences between electroplating and PVD processes. Electroplating is generally more cost-effective and .
pvd coating vs anodizing Powder coating often offers a wider variety of color options. It hides imperfections in the base material, while anodizing provides a rich, metallic finish. In most cases, anodizing is more expensive than powder coating. Still, anodizing is a good option for coating aluminum in a high-traffic environment, or projects with smaller batches.
$280.00
pvd coating vs anodizing